
Fassett Farm Nursery in Jaffrey focuses on native plants
Fassett Farm Nursery in Jaffrey, which has a focus on growing and selling native plants, is back for its second season starting May 4 with a new storefront, expanded hours and new consultation offerings.The nursery is owned by Aaron Abitz, and run on...

UPDATE: Drivers identified in Jaffrey dump truck crash
A collision between a sedan and a dump truck on Route 202 in Jaffrey Wednesday afternoon caused a significant fuel spill across the highway and led to one driver being taken to the hospital.According to police reports, a 2023 Nissan Rogue, driven by...
Most Read
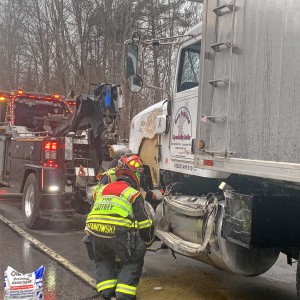


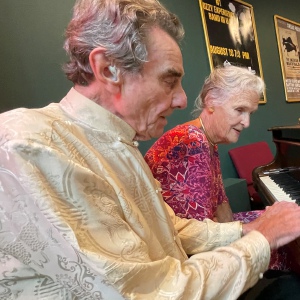


Editors Picks

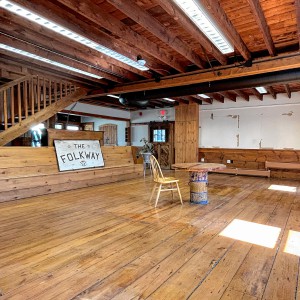


Sports

Katalina Davis dazzles in Mascenic shutout win
The Mascenic softball team soared to a 7-0 shutout win over regional and interdivisional rival Conant thanks to a dazzling performance on both sides of the ball from senior pitcher Katalina Davis. “When Kat’s on, they’re not hitting, so she was...



Opinion

Opinion: It’s time to properly fund education
Susan McKevitt lives in Bradford. On April 11, the New York Times ran an article entitled: “It’s Time to End the Quiet Cruelty of Property Taxes.” Like many towns, Bradford recently had its town meeting, and we experienced this cruelty.Over 200...

Business

BUSINESS QUARTERLY: Grants allow towns to study housing
In 2022 the State of New Hampshire, in recognition of the housing shortage in the state, created a grant program to fund work in towns that wished to explore the housing situation in their town and consider ways to increase housing availability and...



Arts & Life
Greenfield Roadside Roundup is April 27
The Greenfield Conservation Commission will hold its annual Roadside Roundup in honor of Earth Day Saturday, April 27, rain or shine.People can get their blue bags from the Recycling Center, Stephenson Memorial Library, Greenfield Post Office or...




Obituaries
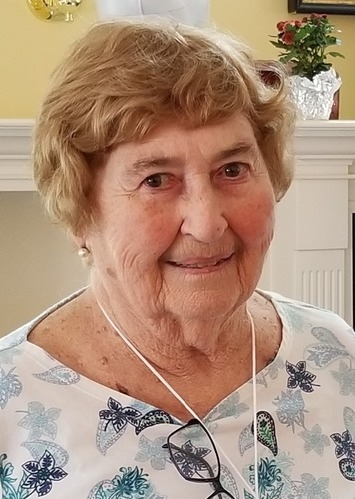
Boscawen, NH - Elizabeth "Betty" G. Mahon, age 93, passed away peacefully on Saturday, April 13, 2024 with family by her side. She was born in Salem, MA daughter of the late John and Elizabeth (Tansey) Gannon. She was predeceased by he... remainder of obit for Elizabeth "Betty" G. Mahon
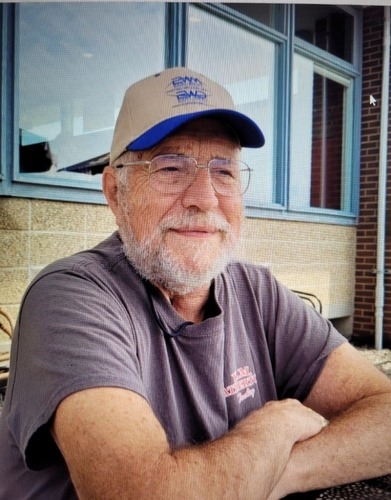
Bennington NH - Phillip A Avery, 81, of Bennington, peacefully passed away on April 4,2024 after a long and hard-fought battle with cancer, while under hospice care at Monadnock Community Hospital with his wife Ann and the love of his f... remainder of obit for Phillip A. Avery
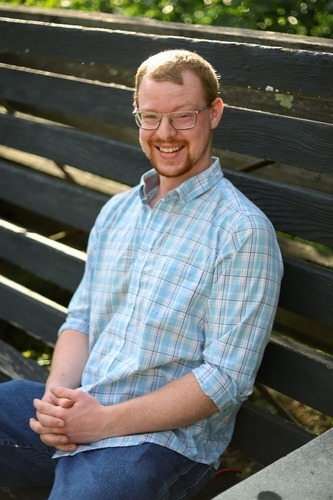
Kevvin W. Sawtelle, 31 Jaffrey, NH - Kevvin W. Sawtelle, 31, of Rindge, died peacefully on April 5, 2024, in the arms of his family at the Dartmouth-Hitchcock Medical Center in Lebanon, NH after a long battle with brain cancer. Kevvin w... remainder of obit for Kevvin W. Sawtelle 31
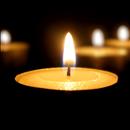
Westmoreland, NH - Constance Marie (Wilson) Boldini, died April 16, 2024. She is predeceased by her husband Guido Boldini and her son Peter Vaillancourt. She is survived by two daughters, Anne Young of Tennessee, Brenda Bryer of Stoddar... remainder of obit for Constance Boldini